1.High Chromium cast iron secondary composite roller tire material
High chromium cast iron ceramic composite roller sleeve is made of high chromium cast iron as matrix material, through special process, high chromium cast iron and honeycomb ceramic particles composite molding, ceramic ZTA ceramic particles, and then through sand casting process, high chromium cast iron ceramic composite and ductile iron secondary composite molding. The chemical composition of high chromium cast iron material is shown in Table 1 below.
Table1:Chemical composition of high chromium cast iron composite roller(wt%)
Material |
C |
Si |
Mn |
S |
P |
Cr |
High chromium cast iron ceramic composite roller tire |
2.8-3.2 |
0.5-1.0 |
0.5-1.2 |
≤0.05 |
≤0.05 |
20-26 |
Ductile iron |
3.2-3.9 |
2.5-2.7 |
0.3~0.5 |
≤0.04 |
≤0.04 |
2.Mechanical property
High chromium cast iron ceramic composite roller tire is a secondary composite molding of high chromium cast iron, ZTA ceramic particles and ductile iron, which makes the ceramic composite roller sleeve not only has high strength and hardness, but also has high toughness, ensuring the wear resistance and safety of the roller sleeve. ZTA ceramic particle hardness is above HV2100, while high chromium cast iron M7C3 carbide hardness is above HV1400, and high chromium cast iron matrix hardness is above HV750, therefore, under the condition of high stress abrasive two bodies high stress wear, due to the difference in materials, the service life of ceramic composite roll sleeve is 1.5-3 times that of ordinary high chromium cast iron roll sleeve. The properties of high chromium cast iron and ductile iron are shown in Table 2 below.
Table 2 :Mechanical Property
Material |
Tensile strength /Mp |
Impact Toughness J/cm 2 |
Hardness/HRC |
Rate of Elongation(%) |
High Chrome |
≥800 |
≥4 |
≥60 |
--- |
Ductile Iron |
500~650 | ---- |
147~241(HB) |
4~10 |
3. Structure design of high chromium cast iron ceramic composite roller tire
The structural design of the high chromium cast iron ceramic composite roller sleeve is shown in Figure 1 and Figure 2 below. The red honeycomb area is the ZTA wear-resistant ceramic particle distribution area. The ceramic particles are distributed in the high chromium alloy matrix in a honeycomb structure, and the ceramic layer covers the working wear area of the whole roller sleeve. The green area outside the ceramic layer is high chromium cast iron, and the blue area is ductile iron.
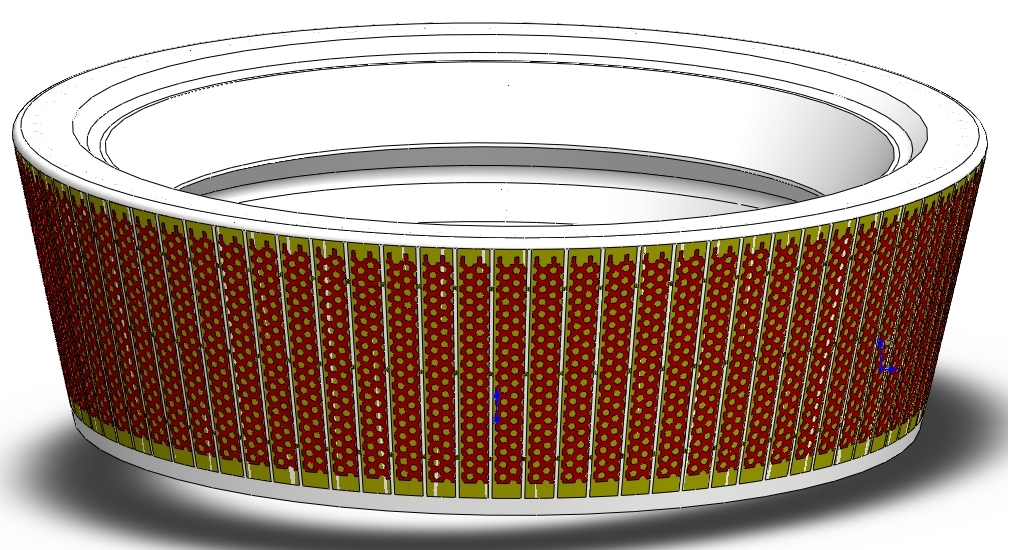
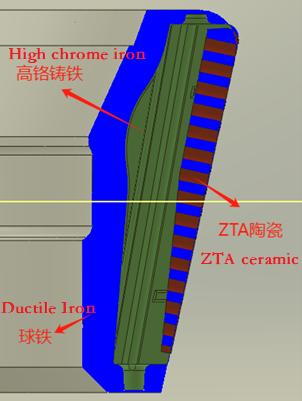